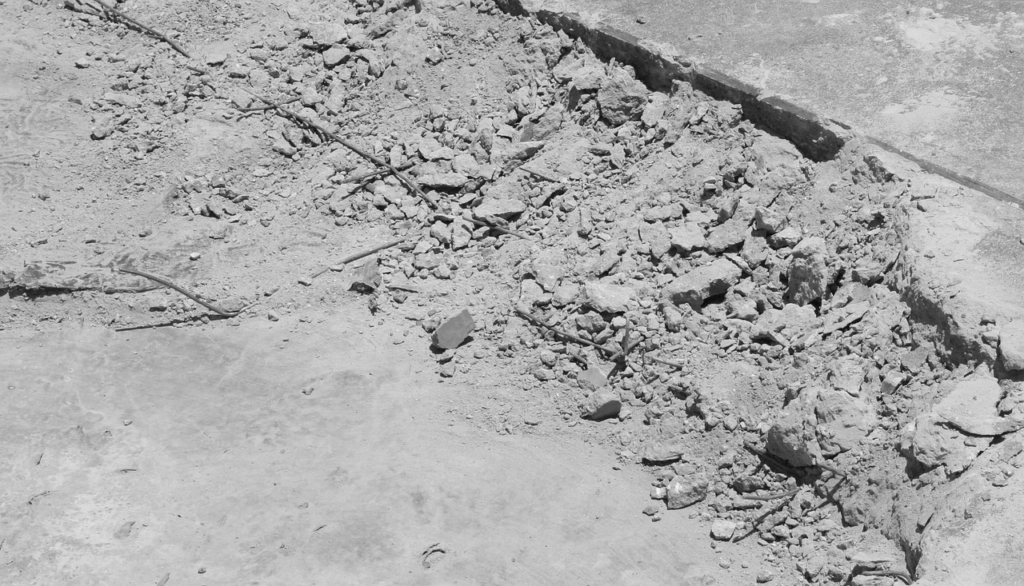
Cement is an integral part of the modern world, serving as the backbone for many of the buildings, bridges, and roads we use every day. But have you ever wondered how this essential material is made? The journey from raw materials to cement is a fascinating process that combines natural resources, chemical reactions, and industrial ingenuity.
In this article, we’ll break down how cement is made, exploring each step of the process, from quarrying raw materials to the final grinding that produces the fine powder ready for construction.
Read
- 1 1. Raw Materials: The Building Blocks of Cement
- 2 2. Crushing and Blending: Breaking Down the Raw Materials
- 3 3. The Kiln: Heating the Mixture to Form Clinker
- 4 4. Cooling and Storing the Clinker
- 5 5. Grinding the Clinker: Producing the Final Cement Powder
- 6 6. Quality Control and Testing: Ensuring Cement Meets Standards
- 7 Conclusion: Cement’s Journey from Quarry to Construction
- 8 Q&A
1. Raw Materials: The Building Blocks of Cement
The first step in cement production is gathering the necessary raw materials. Cement is primarily made from limestone, a sedimentary rock rich in calcium carbonate, and a combination of other materials, such as clay, shale, silica sand, and iron ore.
Why These Materials?
- Limestone provides calcium, a key component in the chemical reaction that creates cement.
- Clay contributes silica, alumina, and iron, essential for the chemical bonding process.
- Sand offers additional silica, while iron ore adds iron, both critical for the strength and color of the cement.
These materials are typically quarried from open-pit mines. Large machines are used to extract and transport the rocks to the cement plant, where the transformation begins.
2. Crushing and Blending: Breaking Down the Raw Materials
Once the raw materials have been collected, they need to be broken down into smaller, more manageable pieces. This is done in two stages: crushing and blending.
Crushing:
The first stage involves using powerful crushers to reduce the limestone, clay, and other materials into smaller chunks. These crushers typically employ rotating drums with steel balls or heavy plates to pulverize the materials into manageable pieces.
Blending:
After crushing, the materials are blended in precise proportions to create a uniform mixture. This is critical because the final quality of the cement depends on the correct balance of raw ingredients. The blended material, known as raw meal, is then transported to the next phase—heating.
3. The Kiln: Heating the Mixture to Form Clinker
The heart of the cement-making process lies in the kiln, an enormous cylindrical furnace that heats the raw meal to temperatures reaching up to 1450°C (2640°F). At this intense heat, chemical reactions occur that transform the raw materials into a new substance known as clinker, the key intermediate in cement production.
The Chemical Reactions:
Inside the kiln, a series of complex reactions take place. The calcium from the limestone reacts with the silica and alumina from the clay to form compounds called calcium silicates. These silicates are the primary binding agents in cement.
The heat drives off carbon dioxide from the limestone in a process called calcination, leaving behind calcium oxide. This reacts with the other materials to form clinker nodules—small, hard lumps that are dark gray in color.
Kiln Design:
Most kilns are equipped with rotating cylinders, tilted slightly so the material slowly moves through the kiln as it rotates. This ensures even heating and efficient reactions throughout the process.
4. Cooling and Storing the Clinker
Once the clinker is formed, it’s still incredibly hot—around 1000°C (1832°F). Before it can be used in the final stages of cement production, the clinker must be cooled rapidly. Cooling is typically done using powerful air fans that lower the temperature to around 100-200°C (212-392°F) in a matter of minutes.
After cooling, the clinker is stored in large silos until it’s ready for the next phase—grinding.
5. Grinding the Clinker: Producing the Final Cement Powder
The final step in the cement-making process is grinding the cooled clinker into a fine powder. This is done using large milling machines, often filled with steel balls or rollers that crush the clinker into an ultra-fine texture. The fine powder is what we know as cement.
Adding Gypsum:
During the grinding process, a small amount of gypsum (a soft sulfate mineral) is added to the clinker. Gypsum plays a crucial role in controlling the setting time of the cement. Without it, cement would set almost immediately after mixing with water, making it nearly impossible to work with.
The result of this grinding process is the fine gray powder that we recognize as cement. This powder is then packed in bags or stored in bulk, ready for shipment to construction sites around the world.
6. Quality Control and Testing: Ensuring Cement Meets Standards
Before cement is distributed to customers, it undergoes rigorous quality control testing to ensure it meets specific industry standards. Tests are conducted to assess the cement’s fineness, setting time, strength, and chemical composition. Consistency is key, as any variation in quality could affect the performance of the final concrete mix.
Conclusion: Cement’s Journey from Quarry to Construction
Cement production is a complex process that transforms basic natural resources into one of the most essential materials for modern construction. From the quarrying of raw materials to the high-temperature kiln reactions that create clinker, every step is vital to producing high-quality cement. The final product, a fine powder, is what enables the creation of concrete, the foundation of our buildings, roads, and bridges.
Next time you pass by a construction site or walk on a concrete sidewalk, you’ll know just how much science, engineering, and raw material go into producing the cement that holds our world together.
Q&A
Q: What’s the difference between cement and concrete?
A: Cement is an ingredient used to make concrete. Concrete is a mixture of cement, water, and aggregates like sand or gravel. Cement acts as the binding agent that holds the mixture together when it sets.
Q: Can cement production be harmful to the environment?
A: Yes, cement production is energy-intensive and emits large amounts of CO2, primarily from the calcination process in the kiln. The industry is exploring ways to reduce emissions, such as using alternative fuels and improving energy efficiency.
Q: What is Portland cement?
A: Portland cement is the most common type of cement used in construction. It’s made by heating limestone and clay at high temperatures to form clinker, which is then ground into a fine powder.
Q: How long does it take for cement to set?
A: Cement begins to set within a few hours of mixing with water, but it can take several weeks to fully cure and reach maximum strength.
Cement is made through a detailed process involving the extraction of raw materials like limestone and clay, crushing and blending them, heating them in a kiln to create clinker, and then grinding the clinker into fine powder. This essential material forms the foundation for concrete, enabling the construction of everything from homes to highways.
Leave a Reply