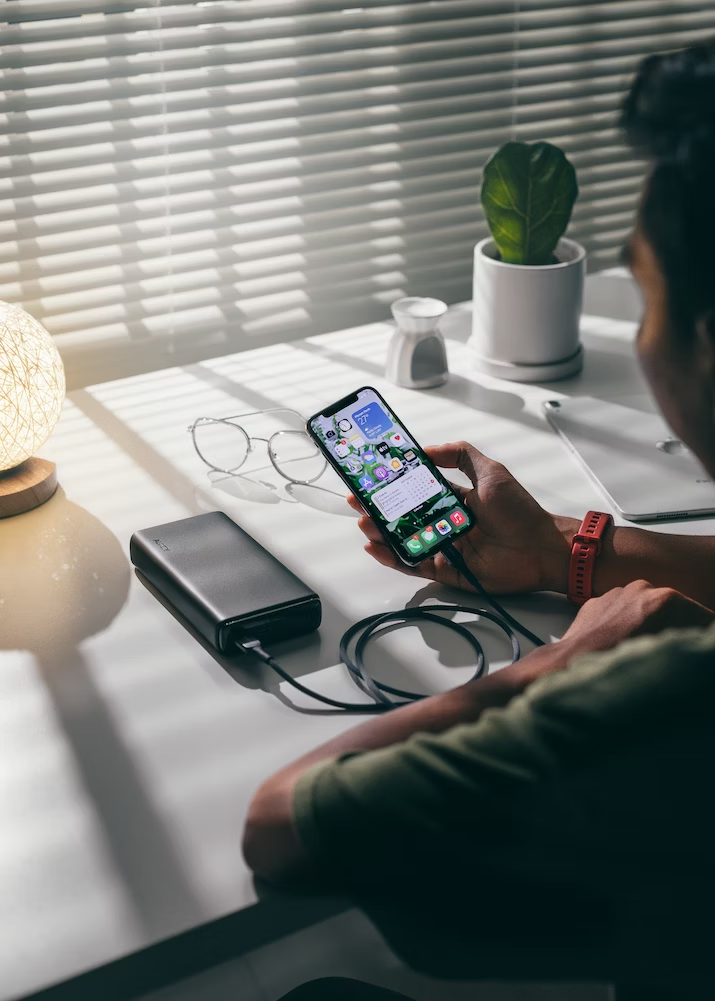
In today’s digital age, where smartphones, tablets, and other portable devices are integral parts of our lives, power banks have become essential accessories. These portable chargers provide us with the convenience of charging our devices on the go. But have you ever wondered how these small and powerful devices are made? Let’s delve into the manufacturing process of power banks.
Read
Components of a Power Bank
Before we dive into the manufacturing process, it’s important to understand the main components of a power bank:
- Battery Cells: These are the heart of any power bank. They store the electrical energy that will be used to charge other devices. The most common types of battery cells used in power banks are Lithium-ion and Lithium-polymer cells.
- Protection Circuit Module (PCM): This component controls the charging and discharging process to protect the battery cells from overcharging, over-discharging, short circuits, and overheating.
- Casing: This is the outer shell that houses all the internal components. It is usually made of durable materials like plastic or metal to protect the internal components from damage.
- Input and Output Ports: These allow for the charging of the power bank itself and the charging of other devices.
- LED Indicators: These show the charging status and the remaining power level of the power bank.
Manufacturing Process
Battery Cell Production
The production of power banks begins with the manufacturing of battery cells. For Lithium-ion or Lithium-polymer cells, this involves several steps including electrode preparation, cell assembly, formation, and aging. The electrodes (anode and cathode) are coated with active materials that allow for the movement of lithium ions, which is the basis for the charging and discharging process.
Assembly of the Protection Circuit Module
The Protection Circuit Module (PCM) is assembled separately. It includes a small circuit board with various electronic components that control the charging and discharging process and provide protection for the battery cells. The PCM is connected to the battery cells, usually by soldering.
Casing Preparation
The casing of the power bank is designed and manufactured separately, often through processes like injection molding for plastic casings or machining for metal casings. The casing is designed to securely house the battery cells and PCM, and to provide openings for the input and output ports and LED indicators.
Final Assembly
In the final assembly process, the battery cells and PCM are placed inside the casing. The input and output ports and LED indicators are installed, and all components are connected. The casing is then sealed, often with screws or adhesive.
Quality Control and Testing
Before the power banks are packaged and shipped, they undergo rigorous quality control and testing. This includes testing the charging and discharging functionality, the protection features of the PCM, and the physical durability of the casing.
The manufacturing of small and powerful power banks involves a complex process of assembling various components, each with its own production process. The result is a convenient device that allows us to keep our digital devices powered on the go. As technology continues to advance, we can expect power banks to become even smaller and more powerful in the future.
Sources:
Leave a Reply